A lower-priced product may not be so economical after all. Mölnlycke promotes greater product and operational efficiencies through product standardization, optimal product utilization and higher care consistency.
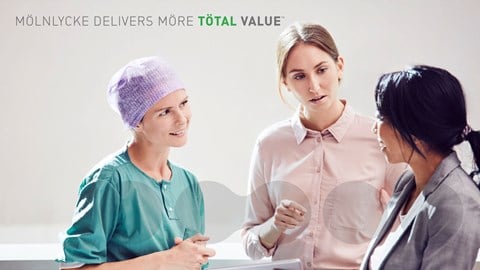
Standardization saves time and money in unexpected ways
Health systems can achieve significant healthcare cost reduction through product standardization to decrease redundancy and focus only on solutions proven to be the most clinically effective and cost-efficient. For one medical center, we initiated a hospital standardization program to reduce surgical gloves SKUs ⏤ taking the OR from 13 gloves and 4 manufacturers to 3 Mölnlycke synthetic Biogel®️ gloves. This made it easier to pull a latex-free option from the shelf, eliminating a recurring problem of latex allergy among staff that halted 30-90 surgical cases annually and prompted costly teardowns. After standardizing, tear downs dropped to zero, representing $43,020 in cost avoidance and 36-60 fewer staff hours over one year.
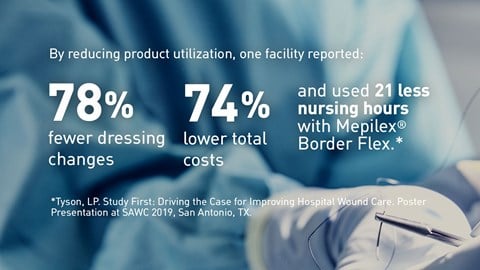
Fine-tune product utilization to drive higher value
Saving a few pennies on a single dressing might cost you more if you have to use more of them per patient. We design our products to optimize efficiency in both acute and post-acute settings. Our Mepilex® Border Flex foam dressings are shown to stay on longer and better adhere to patients' skin, with flexibility in all directions. Clinicians can confidently increase the time between dressing changes without sacrificing patient comfort.
*reference in image
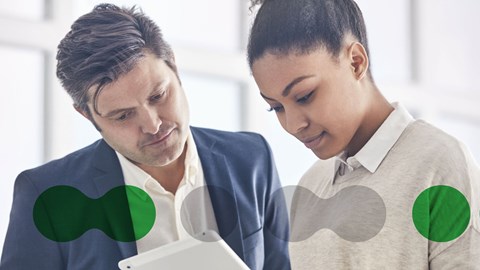
A major product overhaul leads to huge impacts
After reducing their inventory of advanced wound care products by 50%, a Mississippi medical center:
- improved healing rates from 48.4% to 87.5%
- increased patient satisfaction by 13%
- saved $300,000; and
- decreased the time required for product education
'References'